PLC回原点程序的常见问题与解决方案 (plc回原点指令)
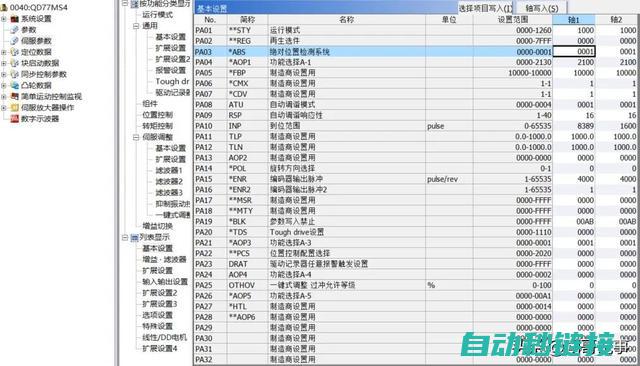
一、引言

在工业自动化领域,PLC(可编程逻辑控制器)作为核心控制设备,广泛应用于各种生产设备的控制系统中。
回原点程序是PLC控制中的一种重要功能,用于设备定位及起始点识别。
在实际应用中,PLC回原点程序常常会遇到一些问题,影响设备的正常运行。
本文将针对PLC回原点程序的常见问题进行分析,并提出相应的解决方案。
二、PLC回原点程序概述
PLC回原点程序是指通过编程实现设备在运行时能够自动返回到设定的原点位置,以便于下一次的准确运行。
回原点功能通常应用于机械设备、生产线、机器人等领域。
在PLC控制系统中,回原点指令是实现这一功能的关键。
通过发送回原点指令,PLC可以控制设备按照预设的路径和方式返回原点。
三、常见问题及原因分析
1. 回原点失败
问题表现:设备在执行回原点程序时无法准确返回到原点位置。
原因分析:
(1)原点位置设定错误:原点位置设置不准确或错误,导致设备无法正确识别。
(2)传感器故障:用于检测设备位置的传感器可能发生故障,导致PLC无法获取准确的设备位置信息。
(3)机械故障:设备机械部分可能存在故障,如传动系统、导轨等,影响设备的正常运行和定位精度。
2. 回原点速度慢
问题表现:设备在执行回原点程序时速度较慢,无法满足生产需求。
原因分析:
(1)程序设置不合理:回原点程序中速度设置不合理,导致设备运行速度过慢。
(2)负载过重:设备在执行回原点程序时负载过重,影响运行速度。
(3)驱动器问题:PLC驱动器或电机驱动器可能存在问题,影响设备的运行速度。
四、解决方案
针对以上问题,我们可以从以下几个方面着手解决:
1. 回原点失败解决方案
(1)检查并重新设定原点位置:确保原点位置设置正确无误,可以根据设备实际情况进行调整。
(2)检查传感器:对用于检测设备位置的传感器进行检查和维护,确保其正常工作。如有必要,更换故障传感器。
(3)检查机械部分:检查设备的机械部分,如传动系统、导轨等,确保其正常运行。如有故障,及时进行维修或更换。
2. 回原点速度慢解决方案
(1)优化程序设置:根据设备实际情况,合理设置回原点程序中的速度参数,提高设备运行效率。
(2)减轻负载:优化生产流程,减少设备在执行回原点程序时的负载。
(3)检查驱动器:对PLC驱动器及电机驱动器进行检查和维护,确保其正常工作。如有故障,及时更换。
五、实例分析与应用技巧
以某生产线上的机器人回原点程序为例,当机器人完成一项任务后需要返回原点以便进行下一项任务。
在实际应用中,可能会出现回原点失败或速度慢的问题。
针对这些问题,我们可以采取以下措施:
1. 确保原点位置设定正确,可以通过调试程序或调整机械结构来实现。
2. 检查光电开关等传感器的工作状态,确保其能够准确检测机器人的位置。
3. 优化回原点程序中的速度设置,根据机器人负载和实际情况进行调整。
4. 定期检查和维护机器人的传动系统、导轨等机械部分,确保其正常运行。
六、结论
PLC回原点程序在工业自动化应用中具有重要意义。
针对回原点程序中常见的问题,我们可以通过检查设定、传感器、机械部分以及优化程序设置等方面来解决。
在实际应用中,还需根据设备实际情况和需求进行调整和优化。
希望通过本文的介绍和分析,能够帮助读者更好地理解和应用PLC回原点程序,提高设备的运行效率和稳定性。
本文地址: http://lh.zdmlj.com/article/21b62687f41ad4ba4f9e.html